In a fast-moving world where consumer needs, demands, and expectations are constantly evolving, Food and Beverage (F&B) manufacturers must remain innovative and flexible. To stay competitive, companies need to adapt processes that help them deliver high-quality, safe, and compliant products—while still getting to market quickly.
However, producing quality food and beverage products is a complex process, filled with potential roadblocks that can slow or even halt operations. So, how can manufacturers stay ahead of the curve, and where should they start?
Discover more in the webinar Harnessing Informatics to Meet Changing Food & Beverage Consumer Expectations, hosted by NewFood. In the webinar F&B industry experts, including STARLIMS own Chief Strategy & Marketing Officer, Brandon Henning, explore key trends in F&B, the impact of changing consumer demands on operations, and how manufacturers can leverage informatics technology to boost efficiencies, accelerate innovation, and get new products to market faster.
The Webinar Agenda
- Adapt to Evolving Market Demands: Discover how industry leaders are staying ahead by aligning operations with shifting consumer expectations and preferences.
- Leverage Cutting-Edge Technology: Explore the role of informatics, predictive analytics, and real-time data in streamlining production, improving quality, and ensuring compliance.
- Implement Best Practices for Success: Gain actionable insights and strategies to optimize your processes, boost sustainability, and accelerate new product introductions (NPI).
Informatics is reshaping the Food & Beverage industry, helping companies stay ahead of changing consumer demands while driving sustainability and efficiency.
Watch the full webinar for deeper insights or check out the highlights below!
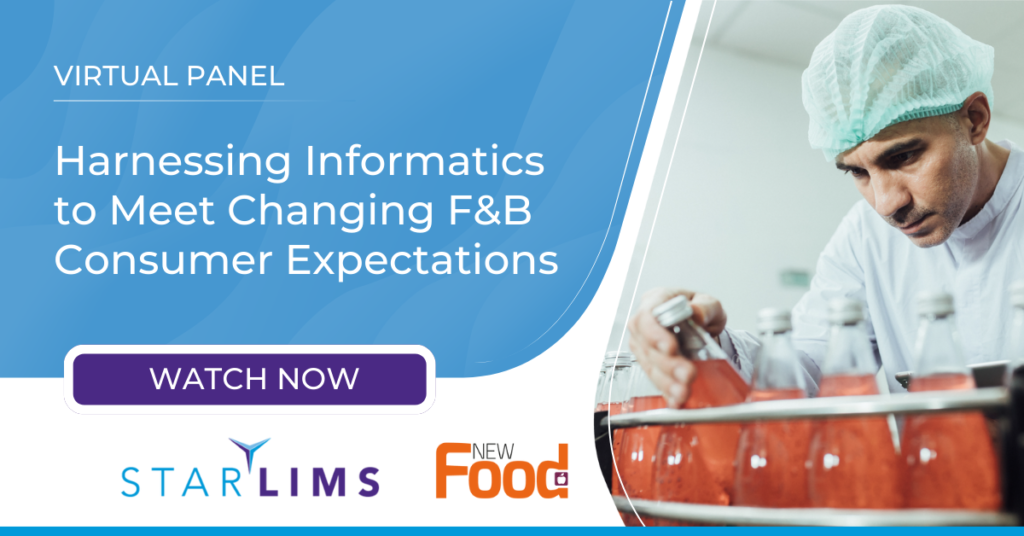
F&B Industry Experts
- Brandon Henning – Chief Strategy & Marketing Officer, STARLIMS
- Lee Reece – Global Food Safety and Quality Improvement Manager, Kraft Heinz
- Adeniyi Odugbemi – Global Director of Food Safety, ADM
Changing F&B Consumer Trends and Operational Impacts
Consumer behavior is shifting toward demanding higher quality and transparency. Lee Reese from Kraft Heinz, explained:
“One of the things we’ve definitely seen over the last few years is a huge increase in demand from consumers for quality and consistency in our products. We used to be very happy with the high standards we had—really high standards—but now we have to push them even further. We didn’t think we could improve much more, but by using better data and systems, we’ve been able to spot gaps and take feedback directly from consumers and customers. That’s really helped us improve in ways we didn’t expect. Improving consistency has become a big focus for us.
We’re also seeing consumers demand different types of products, like more natural formulations with simple, store cupboard ingredients. They want fewer additives, especially ones they see as unhealthy. That’s been a real challenge from the production side—figuring out how to make those products safely without the ingredients we used to rely on. Taking those ingredients out makes things harder, but we still have to produce food that’s just as safe and high-quality as ever.”
Similarly, there is increased demand for increased for new formulations and the ability to manage them dynamically. Brandon Henning explains what he has learned from the STARLIMS F&B customer base and others in the industry:
“There’s a real need for the ability to dynamically manage new formulations. This includes working with different types of products, new additives, and ingredients that manufacturers might not have used before. A big challenge is moving quickly from pilot production to full-scale manufacturing with these new formulations. Whether it’s for a brand-new product or an update to an existing one, we’ve seen customers go from managing 100 recipes for a product to 400 recipes for the same product.
Scaling and manufacturing those variations is complex, especially when you’re distributing globally. What a customer wants in the U.S. might be very different from what a customer in Korea expects, even for a similar product. There’s a growing need to expand quality control capabilities and test faster and more efficiently to keep up with these demands.”
Brandon Henning serves as the Chief Strategy and Marketing Officer at STARLIMS, driving the company’s strategic direction and go-to-market initiatives. With over 20 years of experience in product management, marketing, and IT, Henning has developed innovative solutions for regulated industries, including Food & Beverage, Pharmaceuticals, Medical Devices, and Automotive. He began his career in food manufacturing IT at The J.M. Smucker Company, managing systems across 30 sites. His experience with informatics platforms, including Laboratory Information Management Systems (LIMS), laid the foundation for building solutions that align IT innovation with real-world manufacturing needs. Henning has used this expertise to optimize operations, streamline compliance, and enhance product quality.
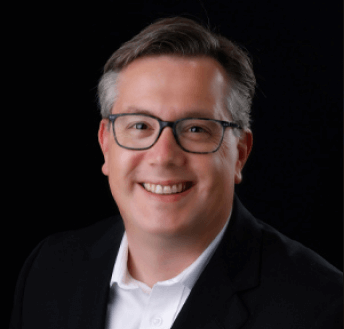
All speakers emphasized that the pace of change is relentless. There’s ever a new ingredient or product that needs to be incorporated safely, and staying ahead means using data and informatics to predict potential issues before they occur.
Boosting Quality Control with Real-Time Data
One of the most significant shifts in F&B manufacturing is the move from post-production testing to in-process testing. This allows manufacturers to make real-time adjustments, minimizing waste and ensuring consistent quality. Reese and Brandon shared how predictive analytics has transformed quality control.
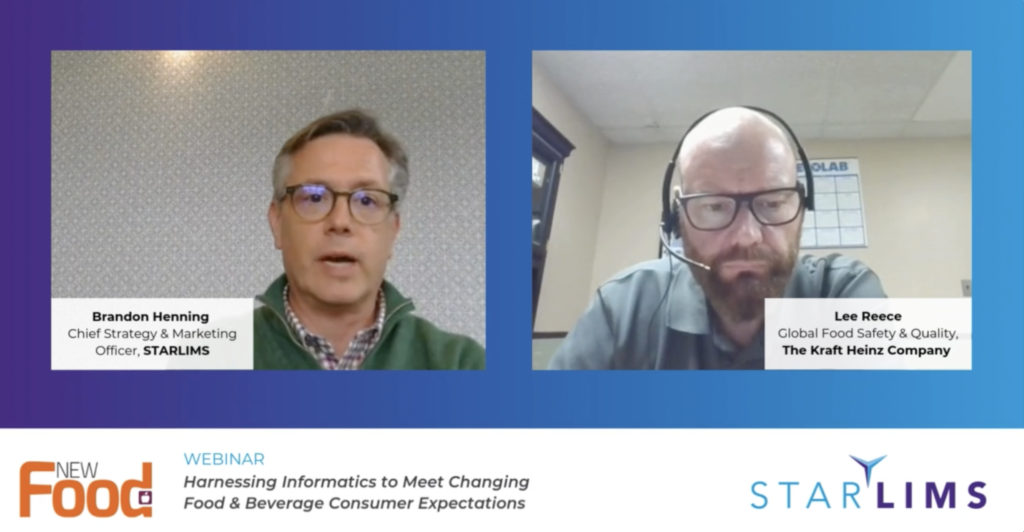
Predictive Analytics: Transforming Manufacturing Efficiency
For many years, quality in manufacturing revolved around the detection and remediation of problems after they occurred. Now, with predictive analytics, Food & Beverage companies can foresee issues and take corrective action. Having predictive models that give companies better foresight into potential future quality problems enables them to make better decisions, faster. All of this has a net positive impact on efficiency and sustainability as well, by preventing waste and reducing environmental impact.
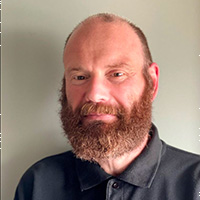
Dr. Lee Reece qualified as a microbiologist and protein chemist working in antiviral and cancer research, before ending up in the food industry by mistake around 25 years ago.
Now happily established in Food Safety and Quality after time spent as a Process Technologist in R&D, he leads a global team of technical experts focusing on Technical Excellence and new technology.
Navigating Technology Adoption Challenges
While informatics systems offer many benefits, implementing them across legacy factories can be challenging. Some facilities, built over a century ago, pose logistical hurdles for modern technology integration. Reese shared
“One of the biggest barriers we’ve faced, to be honest, is the OT (operational technology) capability within some of our factories. A lot of these buildings are 60 to 100 years old—big, solid structures with thick walls—so just getting Wi-Fi and connections to every part of the production line is a real physical challenge. Even something as basic as connecting sensors and making sure they can transmit data is difficult. It’s surmountable, but it takes time, money, and resources, which can be hard to come by. For smaller companies, especially small and medium enterprises, this kind of work can be a real struggle. That said, if they manage to get it done, the advantages are huge, making the effort and investment worthwhile in the end.”
Moreover, as more workers shift toward remote roles, finding talent for manufacturing floors has become difficult. Companies increasingly rely on automation and informatics to fill these gaps, ensuring production continues smoothly without sacrificing quality. According to Henning:
“What we’re seeing is a real decrease in resourcing. It’s getting harder to find people who want to work in quality control, manufacturing, or in the lab. With more jobs going remote, the idea of coming into a factory every day just isn’t as appealing as it used to be.
So, we’re seeing a downturn in resource availability right when there’s an increased need to drive quality. This is pushing quality control departments toward more systematized ways of working—using more data and analytics. To some degree, this shift is helping fill the gaps, allowing companies to maintain high quality with fewer people on site.”
Adeniyi Odugbemi is a seasoned leader in food manufacturing operations, regulatory affairs, and food safety. With extensive expertise in quality control, quality assurance, and supply chain management, Odugbemi has built a reputation for ensuring seamless QA systems and best practices across global food handling operations. His deep knowledge of regulatory compliance spans USDA, FDA, and international standards, making him a trusted authority in navigating complex food regulations. As a proficient auditor, Odugbemi brings comprehensive experience in GFSI frameworks and third-party food facility audits, driving continuous improvement and ensuring adherence to the highest safety and quality standards.
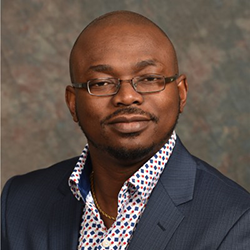
Sustainability Through Smart Manufacturing
Sustainability is on everybody’s minds given the resource-intensive process of food manufacturing. With each batch requiring energy, water, and raw material consumption, getting the batch right the first time is critical. Informatics enable manufacturers with the ability to track batches across their entire production journey, allowing consistency and precision at each step, prevent raw materials spoilage and food waste.
Further supporting sustainability efforts, predictive analytics allow manufacturers to anticipate problems and remediate them, and avoid the wastage in the first place. Predicting failures means less product goes to landfill or down the drain.
Looking to the Future: Democratizing Data and Embracing AI
The future of F&B manufacturing lies in giving operators real-time data access, empowering them to make quick, informed decisions. Reese predicted that operators making on-the-spot decisions will drive efficiency, without waiting for management sign-off. Automation, AI, and machine learning are becoming essential tools for manufacturers seeking to remain competitive, and companies that invest in these technologies today will be better positioned to meet tomorrow’s challenges. Adeniyi Odugbemi also stressed the importance of Informatics in the future of quality control. Listen below:
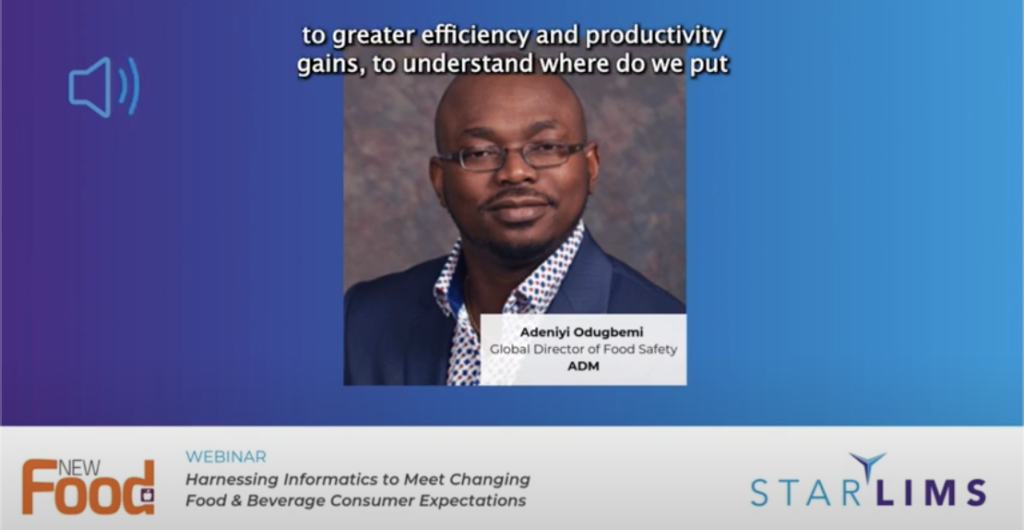
Calculate Your ROI and Start Innovating Today
Ready to unlock the full potential of informatics in your Food & Beverage operations? Use our ROI Calculator to discover the impact the STARLIMS R&D Quality Manufacturing Informatics Platform can have on your bottom line. Whether you’re focused on reducing waste, accelerating new product introductions, or improving regulatory compliance, our calculator will help you understand how informatics can drive value for your business.